Humans find bubbles and other foamy products to be extremely pleasurable, and scientists have long found them to be equally fascinating, owing to the complicated physics at work. A group of Japanese researchers recently published a paper in Scientific Reports describing two distinct mechanisms by which simple foams collapse.
Long-standing questions about the underlying processes that determine the life cycle of liquid foams have been answered by chemical engineers at the University of Illinois Chicago and UCLA. The discovery could aid in the commercial production and application of foams in a variety of industries. The study’s findings were published this month in the Proceedings of the National Academy of Sciences.
Foams are a common occurrence in our daily lives: mixing soaps and detergents into the water while doing dishes, blowing bubbles out of soapy water toys, and sipping the foam of a cup of lattes or milkshakes. Liquid foams can be found in a variety of natural and man-made environments. While some foams form naturally, such as in bodies of water that cause large ocean blooms on beaches, others form as a result of industrial processes. Foams are a byproduct of oil recovery and fermentation, for example.
Chemical engineers have answered longstanding questions about the underlying processes that determine the life cycle of liquid foams. The breakthrough could help improve the commercial production and application of foams in a broad range of industries.
Foams are formed when soapy water is agitated. They are mostly gas pockets separated by thin liquid films that frequently contain micelles, which are tiny molecular aggregates. For example, oily dirt is washed away by hiding in the water-phobic cores of micelles. Furthermore, fat digestion in our bodies is dependent on the role of micelles formed by bile salts.
Foams dissipate over time as the liquid within the thin films is squeezed out. Soap and detergent molecules, which are amphiphilic (both hydrophilic and hydrophobic), aggregate within the water to form spherical micelles, with hydrophilic outward-facing heads and water-phobic tails forming the core.
Ordinary foams, like the head of a glass of beer, and more exotic ones, like solid metallic foams, raise many questions for physicists and have attracted a sizable research community in recent years.
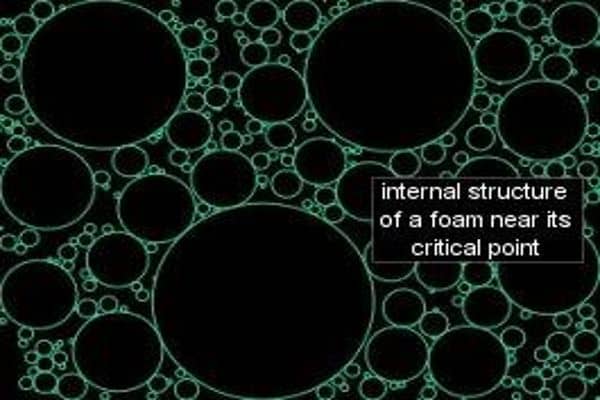
“Micelles are tiny but powerful, not only in cleaning and solubilizing oil-loving molecules but also in influencing flows within foam films,” said co-principal investigator Vivek Sharma, an associate professor of chemical engineering at the University of Illinois at Chicago. He has spent nearly a decade investigating how and why the presence of micelles causes stepwise thinning, or stratification, within ultrathin foam films and soap bubbles.
Sharma and his colleagues developed advanced imaging methods known as IDIOM (interferometry digital imaging optical microscopy) protocols, which are implemented with high-speed and digital single-lens reflex (DLSR) cameras, to solve the puzzle. They discovered that foam films have a rich, ever-changing topography, with thickness differences between strata much greater than micelle size.
“We used a precision technique called small-angle X-ray scattering to resolve the shape, sizes, and densities of the micelles,” said co-principal investigator Samanvaya Srivastava, an assistant professor of chemical and biomolecular engineering at UCLA. “We discovered that the thickness of the foam film decreases in discrete jumps, each jump corresponding to the exact distance between the micelles in the liquid film.”
The researchers also discovered that the arrangement of micelles in foam films is primarily determined by ionic interactions between micelles. The electrostatic attraction and repulsion of ions influence the stability of foams and how their structure decays. With these findings, the researchers determined that by simply measuring the foam film thickness, which can be done with a DSLR camera using the IDIOM protocols, they could characterize both the nanoscale interactions of micelles in liquids and the foam’s stability.
In comparison to previous techniques, which were more time-consuming and required expensive, customized equipment, the new method is not only less expensive but also more comprehensive and efficient.
“The knowledge and understanding could aid in the development of new products ranging from food and personal care to pharmaceuticals,” said the study’s co-lead authors, UCLA Samueli and UIC graduate students Shang Gao and Chrystian Ochoa. “It could also assist engineers in improving foam control in industrial processes.”
The National Science Foundation and the Department of Energy-funded the study, which used the Advanced Photon Source facility at Argonne National Laboratory in Illinois.