Researchers have developed a novel 3D design application that significantly simplifies the wood joining process, while also providing instructions to the milling machines for the efficient production of the designed components. Designs do not require nails or glue, which means that items made with this system can be easily assembled, disassembled, reused, repaired or recycled.
Wood is considered an attractive building material for both esthetic and environmental purposes. The construction of useful wood objects requires complex structures and ways to connect the components together. Researchers have developed a novel 3D design application to greatly simplify the design process and also provide instructions to the milling machine for the efficient production of the designed components. Designs do not require nails or glue, which means that items made with this system can be easily assembled, disassembled, reused, repaired, or recycled.
Researchers from the Department of Creative Informatics at the University of Tokyo have created a 3D design application to create structural wooden components quickly, easily, and efficiently.
Carpentry is a practice as ancient as humanity itself is. Equal to art and engineering, the world around us has been shaped figuratively and literally. Yet, despite its ubiquity, carpentry is a difficult and time-consuming skill, leading to relatively high prices for handmade wooden items such as furniture. For this reason, a lot of wood furniture around us is often, at least to some degree, made by machines. Some machines can be highly automated and programmed with computer-based designs by human designers.
Researchers at the Department of Creative Informatics at the University of Tokyo have developed a 3D design application to create structural wood components quickly, easily and efficiently. They call it Tsugite, the Japanese word for carpentry, and through a simple 3D interface, users with little or no prior experience in either woodworking or 3D design can create designs for functional wood structures in minutes. These designs can then be used to instruct milling machines to carve structural components, which users can then assemble without the need for additional tools or adhesives, following on-screen instructions.
“Our intention was to make the art of carpentry available to people with no specific experience. When the interface was tested in a user study, people new to 3D modeling not only designed some complex structures but also enjoyed doing so “Researcher Maria Larsson said that. “Tsugite is easy to use as it guides users through the process one step at a time, starting with a gallery of existing designs that can then be modified for different purposes. But more advanced users can jump straight to the Manual Edit mode for more freeform creativity.”
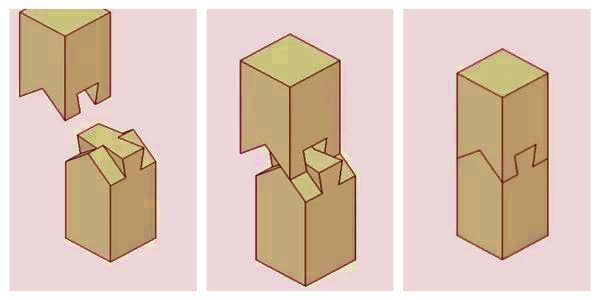
Tsugite provides users with a detailed view of the wooden joints represented by what is known as voxels, essentially 3D pixels, in this case, small cubes. These voxels can be moved around at one end of the component to be joined; this automatically adjusts the voxels at the end of the corresponding component in such a way that they are guaranteed to fit tightly together without needing nails or even glue. Two or more components can be joined together and the software algorithm will adjust all of them accordingly. Different colors inform the user about the properties of the joints, such as how easily they slide together, or problems such as potential weaknesses.
Something that makes Tsugite unique is that it will directly influence the manufacturing process in the designs. This means that milling machines, which have physical limitations, such as their degree of freedom, tool size, and so on, are the only designs they can create. Something that has plagued users of 3D printers, who share a common ancestry with milling machines, is that 3D printer software can’t always be sure how the machine itself behaves, which can lead to failed printing.
“There is some great research in the field of computer graphics on how to model a wide range of joint geometries. However, this approach often lacks practical considerations of manufacturing and material properties, “Larsson said that. “Conversely, research in the fields of structural engineering and architecture may be very thorough in this regard, but it may concern only a few types of joints. We have seen the potential to combine the strengths of these approaches to create Tsugite. It can explore a wide variety of joints and yet keep them within realistic physical limits.”
Another advantage of incorporating manufacturing limitations into the design process is that Tsugite’s underlying algorithms have an easier time navigating all the different possibilities that could be presented to users, as those that are physically impossible are simply not given as options. Through further refinements and advancements, the researchers hope that Tsugite can be scaled up to design not only furniture and small structures, but also entire buildings.
“According to the United Nations, the construction and construction industry is responsible for almost 40% of the world’s carbon dioxide emissions. Wood is perhaps the only natural and renewable building material we have, and efficient carpentry can add additional sustainability benefits,” said Larsson. “For example, when connecting wood with joinery, as opposed to metal fixing, it reduces the mixing materials. It’s good for sorting and recycling. Also, unglued joints can be removed without destroying the building components. This opens up the possibility of buildings being disassembled and reassembled elsewhere. Or to replace the defective parts. This flexibility of reuse and repair adds sustainability benefits to wood.”