Engineers have developed a cutting-edge brain-computer interface with a flexible and moldable backing and piercing microneedles. The addition of a flexible backing to this type of brain-computer interface allows the gadget to conform more evenly to the brain’s complicated curving surface and to distribute the microneedles that pierce the cortex more uniformly.
The microneedles emerge from the flexible backing, penetrate the surface of the brain tissue without penetrating surface venules, and record impulses from neighboring nerve cells equally throughout a vast area of the cortex. So yet, this innovative brain-computer interface has only been tested in rodents.
So yet, this innovative brain-computer interface has only been tested in rodents. The findings were published online in the journal Advanced Functional Materials. A team lead by electrical engineering professor Shadi Dayeh at the University of California San Diego collaborated with researchers at Boston University led by biomedical engineering professor Anna Devor on this work.
This novel brain-computer interface is comparable to, and outperforms, the “Utah Array,” the current gold standard for brain-computer interfaces using penetrating microneedles. The Utah Array has been shown to benefit stroke sufferers and others with spinal cord injuries. People who have Utah Arrays implanted can use their thoughts to control robotic limbs and other equipment, restoring certain daily functions such as moving objects.
These soft-backed brain-computer interfaces are thinner and lighter than typical glass-backed brain-computer interfaces. The researchers write in their work Advanced Functional Materials that light, flexible backings may lessen discomfort of brain tissue that comes into touch with sensor arrays.
The new brain-computer interface has a flexible, conformable, and customizable backing, whereas the Utah Array has a rigid and inflexible backing. The innovative microneedle-flexibility array’s backing’s and conformability supports closer contact between the brain and the electrodes, allowing for better and more uniform recording of brain-activity signals. Working with rodents as model species, the researchers exhibited sustained broadband recordings that produced robust signals for the duration of the implant, which lasted 196 days.
Furthermore, the way soft-backed brain-computer interfaces are made allows for larger sensing surfaces, which implies that a far wider area of the brain surface may be monitored at the same time. The researchers show in their study published in Advanced Functional Materials that a penetrating microneedle array with 1,024 microneedles successfully recorded signals generated by specific inputs from rats’ brains. When compared to current technology, this represents 10 times the number of microneedles and ten times the area of brain coverage.
Thinner and transparent backings
These soft-backed brain-computer interfaces are thinner and lighter than typical glass-backed brain-computer interfaces. The researchers write in their work Advanced Functional Materials that light, flexible backings may lessen discomfort of brain tissue that comes into touch with sensor arrays.
The translucent flexible backings are also available. The researchers show in their new study how this transparency may be used to conduct fundamental brain research with animal models that would otherwise be impossible. For example, the researchers showed simultaneous electrical recording from arrays of penetrating microneedles as well as optogenetic photostimulation.
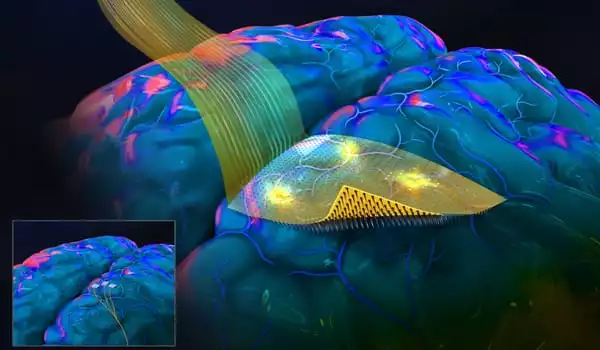
Two-sided lithographic manufacturing
The flexibility, bigger microneedle array footprints, reconfigurability, and transparency of the novel brain sensors are all due to the researchers’ double-sided lithography approach.
The team’s manufacturing approach, which begins with a hard silicon wafer, allows them to manufacture minuscule circuits and devices on both sides of the rigid silicon wafer. On one side of the silicon wafer, a flexible, transparent coating is applied. A bilayer of titanium and gold traces is implanted within this film, so that the traces line up with where the needles will be created on the other side of the silicon wafer.
Working from the other side, all of the silicon is etched away save for free-standing, thin, pointed columns of silicon after the flexible film is applied. These pointed columns of silicon are the microneedles, and their bases align with the titanium-gold traces that remain within the flexible layer after the silicon has been etched away. These titanium-gold traces are patterned using standard and scalable microfabrication processes, which enables scale production with minimum manual effort. The manufacturing technology allows for customizable array design as well as scalability to tens of thousands of microneedles.
Toward closed-loop systems
Penetrating microneedle arrays with large spatial coverage will be required in the future to develop brain-machine interfaces to the point where they can be employed in “closed-loop systems” that can benefit patients with severely limited movement. This type of closed-loop system, for example, may provide a person utilizing a robotic hand with real-time tactical feedback on the objects the robotic hand is holding.
Tactile sensors on the robotic hand would detect an object’s hardness, texture, and weight. The sensors’ data would be transformed into electrical stimulation patterns that would pass through wires outside the body to the brain-computer interface using penetrating microneedles. These electrical signals would transmit information about the object’s hardness, texture, and weight directly to the person’s brain. In turn, the individual would modify their grasp strength depending on information sensed directly from the robotic arm.