Carbon fiber reinforced composites (CFRCs) continue to play a vital role in the growth and advancement of many weight-sensitive industries. However, their growth has raised growing questions about the practices and techniques needed to cope with these costly engineering systems at the end of their life cycle.
Standard carbon-fiber-reinforced polymer (CFRP) composite materials are neither recyclable nor repairable due to the permanently interlinked network of thermoset polymers. Solid and robust as thermoset plastics, and moldable and recyclable as their thermoplastic equivalents, thermocouples provide innovative ways to recycle thermosets and CFR composites.
The WSU researchers used an entirely new matrix polymer material called epoxy vitrimer, which can be recycled or reused more easily. They developed a recyclable carbon-fiber-reinforced composite material that could directly substitute conventional non-recyclable CFRPs into the existing manufacturing processes.
From the aerospace and automobile industry to the building and sports goods production, CFRP composite uses are continually expanding due to the excellent mechanical properties of the material, reduced weight, and increased long-term longevity. The rapid demand for CFRP composites poses significant questions about the availability of cost-effective waste treatment and recycling solutions for these products. Owing to the intrinsic heterogeneity of the thermoset polymer matrix and the reinforcing fibers, the CFRP composites demonstrate low recyclability.
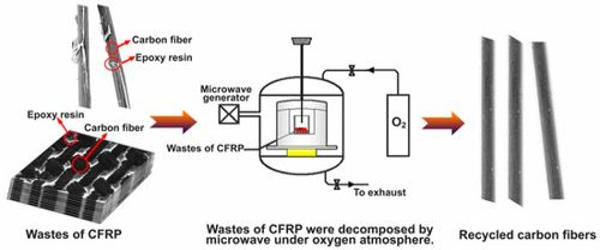
Reducing the Environmental Impact of Carbon-Fiber-Reinforced Composites
At present, such materials are typically down-cycled as fuel for power generation with a little recovery of useful materials such as carbon fiber reinforcement. The ongoing move from a take-up approach to more competitive economic models that will allow raw materials to be used for as long as possible involves the production of advanced recyclable CFRP composites.
Composite materials are composed of at least two distinct elements, thus benefiting from the integration of the properties of each of the components. These materials are normally composed of a reinforcement layer, typically carbon or glass fiber, and a matrix step, which serves as a bond that holds the whole structure together. Components that may improve composite properties, such as fire resistance or electrical conductivity, can also be incorporated.
In traditional CFRP composites, the binder (matrix) elements are typically thermoset polymers, such as epoxy resins. These materials are chosen for their excellent thermal and chemical resistance. Upon curing, thermosetting polymers form an irreversibly interlinked network resulting in a rigid and resilient structure that contributes to the improved strength and resistance of CFPR composites.
However, the disposal of such content is highly difficult and represents a huge challenge. An additional challenge emerges from the need to remove and separate the polymer from the carbon fibers.
Mechanical recycling produces low-quality carbon fibers (CFs) with shorter lengths and lower tensile modules, whereas thermal recycling process, in particular pyrolysis, produces surface-forming carbon fibers. Among them, the most exciting is chemical recycling, as CFs can be recycled from CFREPs very quickly and in the most environmentally safe conditions.
Vitrimer Epoxy Resins Offer New Possibilities for Innovative Composite Materials
A research team led by Professor Jinwen Zhang at the School of Mechanical and Materials Engineering, Washington State University (WSU) in the USA, has developed a recyclable carbon-fiber-reinforced composite material that could directly replace traditional non-recyclable CFRPs with current manufacturing processes.
WSU researchers have used a brand new matrix polymer substance called epoxy vitrimer, which can be recycled or reused more effectively. The term “vitrimer” refers to the vitreous-like thermal behavior of the substance. At high temperatures, the viscosity of the substance reduces and allows heat relief and malleable mechanical properties. Upon freezing, the substance serves as an elastic thermoset (or elastomer).
This helps thermoset plastics to be reprocessed using traditional thermoplastic manufacturing methods, e.g. injection and vacuum molding and extrusion. Vitrimers, unlike thermoplastics, preserve secure intermolecular communication through densely interlinked networks even at elevated temperatures.
Vitrimers consist of a covalent organic network that can rearrange its topology by reversible exchange reactions that maintain the total number of network bonds (or crosslinking density) and their molecular architecture.
Self-Healing High-Strength Composite Materials
Vitrimer epoxy resin synthesized by Professor Zhang’s team does not need an external catalyst for curing reactions. Instead, it relies on an internally catalytic response caused by abundant hydroxyl precursor groups acting as catalytic species to facilitate cross-linking reactions and subsequent exchange reactions. In comparison to the permanent crosslinked networks of traditional epoxy materials, these complex interchange reactions between the polymer chains of the vitrimer allow the internal release of stress associated with the external strain applied while maintaining the crosslinked network.
As a result, the substance exhibits accelerated stress relief and excellent self-healing properties at elevated temperatures (above 150 °C). In order to demonstrate the excellent mechanical properties of the new material, the researchers prepared CFRP composite material with three layers of carbon fiber fabric and Vitrimer Epoxy as a binding matrix.
The new composite CFRP had a tensile strength of 356 MPa, equivalent to that of standard CFRP materials. Heated above the glass transition temperature of the vitrifier (> 200 °C), the composite material displayed a remarkable ability to shift form, unlike the thermoset CFRP composites.