Researchers around the world are currently working on developing very small nanosized robots with a variety of embedded capabilities such as complex electronic circuits, sensors, antennas, and photovoltaics. One of the most difficult techniques that scientists must use with such small robots is to design them to move by bending. The Cornell team was able to develop micron-sized shape memory actuators that allow atomically thin two-dimensional materials to fold into three-dimensional configurations.
Researchers developed micron-sized shape memory actuators that allow atomically thin two-dimensional materials to fold into three-dimensional configurations. All they need is a quick jolt of electricity. And once bent, the material retains its shape even after the voltage is removed.
To create a fully functional nanosized robot, you must include a variety of capabilities, ranging from complex electronic circuits and photovoltaics to sensors and antennas. But, more importantly, if you want your robot to move, it must be able to bend.
Cornell researchers create the world’s smallest origami bird using nanotech. They have created micron-sized shape memory actuators that enable atomically thin two-dimensional materials to fold themselves into 3D configurations.
Cornell University researchers developed micron-sized shape memory actuators that allow atomically thin two-dimensional materials to fold into three-dimensional configurations. All they need is a quick jolt of electricity. And once bent, the material retains its shape even after the voltage is removed. As an example, the team created what could be the world’s smallest self-folding origami bird. And it’s not a joking matter.
The group’s paper, “Micrometer-sized electrically programmable shape memory actuators for low-power microrobotics,” was featured on the cover of Science Robotics. Qingkun Liu, a postdoctoral researcher, is the paper’s lead author.
Itai Cohen, professor of physics, and Paul McEuen, John A. Newman Professor of Physical Science, are leading the project. McEuen and Cohen’s ongoing collaboration has resulted in a slew of nanoscale machines and components, each seemingly faster, smarter, and more elegant than the one before it.
“We’d like to have microscopic robots with brains on board. That means you’ll need appendages powered by complementary metal-oxide-semiconductor (CMOS) transistors, which are essentially a computer chip on a 100-micron-wide robot” Cohen stated.
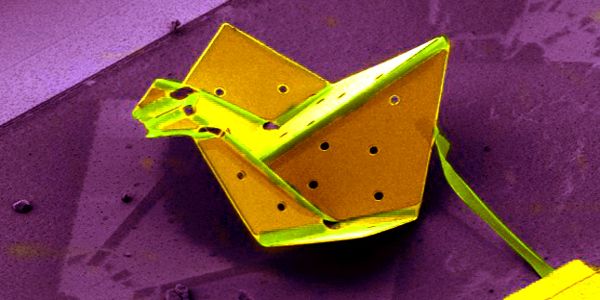
Consider a million fabricated microscopic robots releasing from a wafer, folding themselves into shape, crawling free, and carrying out their tasks, even assembling into more complex structures. That’s the plan. “The difficult part is creating materials that respond to the CMOS circuits,” Cohen explained. “And this is what Qingkun and his colleagues have done with this shape memory actuator that can be driven with voltage and hold a bent shape.”
The machines fold themselves in 100 milliseconds or fewer. They can also fold and flatten themselves thousands of times. And they only require a single bolt to turn on. Guinness World Records has already recognized the team for developing the world’s smallest walking robot. They are now hoping to set a record with a new self-folding origami bird that is only 60 microns wide.
The team is currently integrating their shape memory actuators with circuits to create walking robots with foldable legs as well as sheet-like robots that move forward by undulating. According to Cohen, these advancements could one day lead to nano-Roomba-type robots that can clean bacterial infections from human tissue, micro-factories that can transform manufacturing, and robotic surgical instruments that are ten times smaller than current devices.
“Dr. Cohen and his team are pushing the boundaries of how quickly and precisely we can control motion at the micro- and even nano-scales,” said Dean Culver, program manager for the Army Research Office, a component of the United States Army Combat Capabilities Development Command’s Army Research Laboratory, which funded the research. “In addition to paving the way for nano-robots, scientific advances from this effort can enable smart material design and interaction with the molecular biological world, which can help the Army in ways never seen before.”
The Army Research Laboratory of the United States Army Combat Capabilities Development Command, the National Science Foundation, the Cornell Center for Materials Research, the Air Force Office of Scientific Research, and the Kavli Institute at Cornell for Nanoscale Science all provided assistance. The Cornell NanoScale Science and Technology Facility assisted with some of the work.
The smallest curvature is critical because the size of the robot determines how small the various appendages are controlled in microscopic robot manufacturing; the tighter the bends and the smaller the folds, the smaller the overall footprint of the robot. The bots are made of nanometer-thin platinum layers with a titanium or titanium dioxide film on top. On top of those layers, rigid panels of silica dioxide glass are placed. When a negative voltage is applied to the robot, it returns to its original state.