Dmitry Momotenko, a scientist, led a research team that created a new 3D printing technology for producing ultrasmall metallic objects. The researchers intend to use this technology to significantly expand the surface area of battery electrodes in order to greatly shorten charging times.
Liaisan Khasanova, a chemist, transforms an ordinary silica glass tube into a printing nozzle for a particularly sophisticated 3D printer in less than a minute. The chemist inserts a one-millimeter-thick capillary tube into a blue apparatus, shuts the flap, and presses a button. There is a loud bang after a few seconds, and the nozzle is ready for use.
“Inside the device, a laser beam heats up the tube and pulls it apart.” Then we quickly raise the tensile strain, causing the glass to break in the center and form an extremely sharp tip,” explains Khasanova, who is pursuing an in chemistry at the Electrochemical Nanotechnology Group.
Khasanova and her colleagues require tiny nozzles to print extremely small three-dimensional metallic objects. This means that the apertures in the nozzles must be equally small—in some circumstances, so small that only a single molecule may squeeze through. “We’re trying to push 3D printing to its technological limits,” says Dr. Dmitry Momotenko, who leads the Institute of Chemistry’s junior research group. “We want to assemble objects atom by atom.”
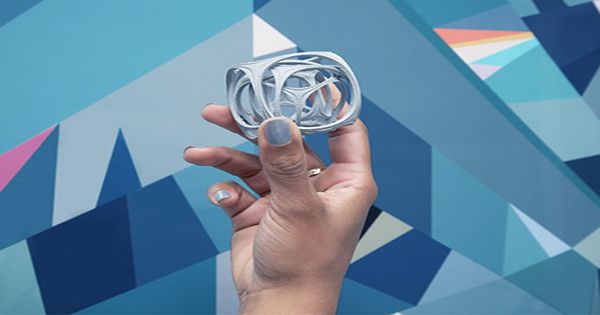
Metals are the perfect solution: The chemist explains that nanoscale 3D printing, or 3D printing of objects a few billionths of a meter in size, opens up incredible possibilities. He sees several possibilities for metal things, particularly in microelectronics, nanorobotics, sensor, and battery technology. “Electroconductive materials are required for a wide range of applications in these fields, so metals are an excellent choice.”
While 3D printing of plastics has already gone to these microscopic proportions, 3D printing of tiny metal items has proven more difficult. Some approaches still produce printed structures that are a thousand times too huge for many modern applications, while others make it impossible to produce objects with the required degree of purity.
Momotenko specializes in electro-plating, which is a type of electrochemistry in which metal ions floating in a salt solution come into contact with a negatively charged electrode. Positively charged ions mix with electrons to generate neutral metal atoms, which form a solid layer on the electrode.
“A liquid salt solution turns into a solid metal—a process that we electrochemists can very effectively control,” explains Momotenko. On a bigger scale, the same procedure is used to chrome-plate automotive parts and gold-plated jewelry.
A little smaller than usual: A visit to the group’s modest laboratory on the Wechloy campus demonstrates that adapting it to the nanoscopic scale requires tremendous imagination, work, and care. According to Momotenko, the lab comprises three printers, all of which were built and programmed by the crew itself. They, like other 3D printers, include a print nozzle, tubes for feeding in the print material, a control mechanism, and mechanical components for moving the nozzle—but everything in these printers is a little smaller.
A colored saline solution flows through delicate tubes into the thin capillary tube, which houses the anode, which is a hair-thin piece of wire. It completes the circuit with the negatively polarized cathode, a gold-plated silicon flake the size of a fingernail that also serves as the printing surface. When an electrical voltage is delivered quickly, micromotors and unique crystals that morph instantly move the nozzle by fractions of a millimeter in all three spatial directions.
Unwanted vibrations: Because even minor vibrations can interrupt the printing process, two of the printers are contained in boxes lined with a thick layer of dark acoustic foam. Furthermore, they are supported by granite plates weighing 150 kilos each. Both approaches are designed to keep unwanted vibrations at bay. Because the electromagnetic fields produced by alternating current from a socket would interfere with the tiny electrical currents and voltages required to operate the nano-printing process, the lamps in the lab are also battery-powered.
Dive deep into the nanoworld: Columns are the most basic geometric patterns produced by 3D printing, but the Oldenburg researchers can also create spirals, circles, and various overhanging structures. Currently, the technology can print with copper, silver, and nickel, as well as nickel-manganese and nickel-cobalt alloys.
They have already descended into the nanoworld in some of their experiments. In a work published in the journal Nano Letters in 2021, Momotenko and an international team of researchers stated that they had constructed copper columns with a diameter of only 25 nanometers, bringing 3D metal printing below the 100-nanometer limit for the first time.
A feedback mechanism that allows precise control of the print nozzle’s movements was one of the success factors. It was created by Momotenko and Julian Hengsteler, a student he oversaw at his previous employer, ETH Zurich in Switzerland. “Continuous retraction of the print nozzle is extremely important because it would quickly become clogged otherwise,” adds the chemist.
Controlling the Invisible: Layer by layer, the team prints the small things at a few nanometers each second. Momotenko is still amazed that items too small to be seen with the naked eye are made here. “You begin with a touchable object. Then something happens, and you can manipulate these unseen things on a very small scale—it’s almost incredible,” adds the chemist.
Momotenko’s intentions for his nano-printing process are similarly impressive. His ambition is to build the groundwork for batteries that can charge 1,000 times faster than existing ones. “If that can be done, you could charge an e-car in seconds,” he says. The fundamental concept he is pursuing is almost 20 years old.
The idea is to substantially shorten the ion routes inside the battery during the charging process. The electrodes, which are currently flat, would need to have a three-dimensional surface structure to do this. “With the current battery design, charging takes so long because the electrodes are relatively thick and spaced so far apart,” adds Momotenko.
He claims that the solution is to interlock the anodes and cathodes like fingers at the nanoscale, reducing the distance between them to a few nanometers. This would allow the ions to flow at breakneck speed between the anode and cathode. The issue is that producing battery structures with the needed micro dimensions has so far proved impossible.
Fabricating battery materials with ultrasmall structural features: Momotenko has now accepted the challenge. The purpose of his NANO-3D-LION project is to create and use advanced nanoscale 3D printing techniques to create active battery materials with ultrasmall structural characteristics.
Momotenko decided to base the study at the University of Oldenburg after previously successfully collaborating with a research group led by Prof. Dr. Gunther Wittstock at the Institute of Chemistry. “The Department for Research and Transfer was very helpful with my grant application, so I moved here from Zurich at the beginning of 2021,” he says.
His research team now has four members, including Khasanova, student Karuna Kanes, and Master’s student Simon Sprengel. Kanes concentrates on a new way of optimizing print nozzle precision, while Sprengel studies the feasibility of printing combinations of two distinct metals—a procedure required to manufacture cathode and anode material in one step.
Liaisan Khasanova’s research will shortly concentrate on lithium compounds. Her objective will be to figure out how to structure the electrode materials now used in lithium batteries using 3D printing. The team intends to examine substances such as lithium-iron or lithium-tin before testing how large the nano “fingers” on the electrode surfaces should be, what spacing is viable, and how the electrodes should be oriented.
The issue of energy storage is complicated: The researcher emphasizes that the problem of energy storage is exceedingly complex, and his team can only play a minor role in fixing it. Nonetheless, he believes his group is off to a strong start: electrochemical 3D printing of metals is presently the only realistic alternative for creating nanostructured electrodes and testing the concept, in his opinion.
Aside from battery technology, the chemist is focusing on other daring ideas. He hopes to use his printing technology to create metal structures that will allow for more precise control of chemical reactions than has previously been feasible.
Such plans play a role in spintronics, a relatively new field of study that focuses on the manipulation of “spin”—a quantum mechanical feature of electrons.
Sensors that detect individual molecules: Another idea he aims to put into action is to create sensors capable of detecting individual molecules. “That would be useful in medicine, for example, for detecting tumor markers or biomarkers for Alzheimer’s disease at extremely low concentrations,” explains Momotenko.
All of these concepts are still relatively novel in the field of chemistry. “It is not yet clear how it would all work,” he concedes. But that’s how science works. “Every meaningful research project necessitates extensive thought and planning, and most ideas fail,” he adds. But they don’t always, and he and his team have already made the first successful steps on their path.