Aluminium oxynitride is a clear ceramic made of aluminum, oxygen, and nitrogen. It’s a clear polycrystalline ceramic with a cubic spinel crystal structure composed of nitrogen, oxygen, and aluminum. In the near-ultraviolet, visible, and infrared ranges. It is four times stronger than fused silica glass, eighty-five percent stronger than sapphire, and fifteen percent stronger than magnesium aluminate spinel.
In the near-ultraviolet, visible, and mid-wave-infrared areas of the electromagnetic spectrum, ALON is optically transparent (≥ 80%). It is four times harder than fused silica glass, eighty-five percent harder than sapphire, and roughly 115 percent harder than magnesium aluminate spinel. Since it has a cubic spinel structure, it can be fabricated into transparent windows, plates, domes, rods, tubes, and other forms using conventional ceramic powder processing techniques.
Properties
The material remains solid up to 1200°C (2190°F). It has good corrosion resistance and resistance to damage from radiation and oxidation. It is about three times harder than steel of the same thickness.
- Molecular Weight: N/A
- Appearance: White to transparent solid
- Melting Point: ~2150 °C
- Boiling Point: N/A
- Density: 3.696-3.691 g/cm3
- Solubility in H2O: Insoluble
- Crystal Phase / Structure: Cubic, spinel
- Thermal Conductivity: 13 W/mK
- Young’s Modulus: 323 GPa
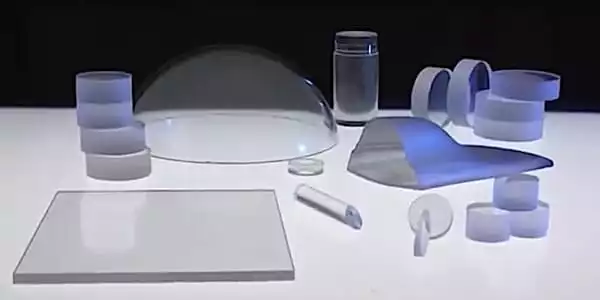
ALON is the hardest polycrystalline transparent ceramic on the market. It offers potential for applications such as bulletproof, blast-resistant, and optoelectronic windows due to its low weight, distinct optical and mechanical qualities, and resistance to oxidation or radiation. Multiple armor-piercing rounds of up to.50 BMG caliber have been shown to be stopped by ALON-based armor.
ALON is commercially available in sizes as large as 18-by-35-inch (460 mm × 890 mm; 46 cm × 89 cm) monolithic windows.
Production Method
The created ceramic material is subjected to elevated temperature heat treatment before being ground. After then, the material is polished to make it more transparent. Around 2100°C (3812°F), it loses transparency. Grinding and polishing primarily improve impact resistance, resulting in a material that is 85 percent tougher than sapphire and 15 percent harder than magnesium aluminate spinel.
A sintering additive is added to a source powder that contains less than 0.5 weight percent MgO in this approach. The source powder is then presintered at temperatures ranging from 1550 to 1750°C (2822 to 3182°F) to produce a cubic-phased polycrystalline aluminum oxynitride ceramic with a relative density of greater than 95%. The source powder can be again sintered at 1900°C (3452°F) in order to further increase the relative density of the material. As a result, the porosity is eliminated and the transparency increases to more than 95%.
Applications
ALON is utilized for infrared-optical windows, with better than 80% transparency at wavelengths less than 4 micrometers and approaching zero at 6 micrometers. As a result, it has uses as a sensor component, customized IR domes, and laser communications windows. It has also been demonstrated in various semiconductor-related applications as an interface passivation layer.
Some Common applications are –
- Semi-conductor related applications
- Insulators and heat radiation plates
- Optoelectronic devices
- Power and multichip modules
- Translucent ceramics
- High temperature materials and heat sinks
- Break rings
- Thermally conductive filler.